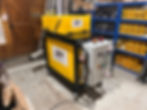
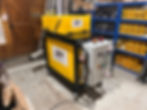
Epot OPM:
The revolutionary, all electric optical pitch melter
WHAT IS IT?
The Epot OPM is an electrically controlled, compound heater which has been designed for the melting and heating of pitch compounds used in precision laser levelling and polishing.
The Epot OPM heats pitch compounds quickly and efficiently. Control software maintains the manufacturer’s predetermined temperature throughout its operation, thereby delivering a quality assured product. The risk of ‘flash’ and vapour ignition fires caused by overheating is eliminated.
An abundance of safety features is built into these impressive pieces of equipment which not only keeps the user safe but delivers product in a fast, efficient, timesaving and carbon friendly manner.
Unique features including an automatic lift system, auto control agitator, and swivel spout, allow users to melt, raise and pour pitch in one motion.